A Q&A to discover MAELSTROM’s Robotic Seabed Cleaning Platform
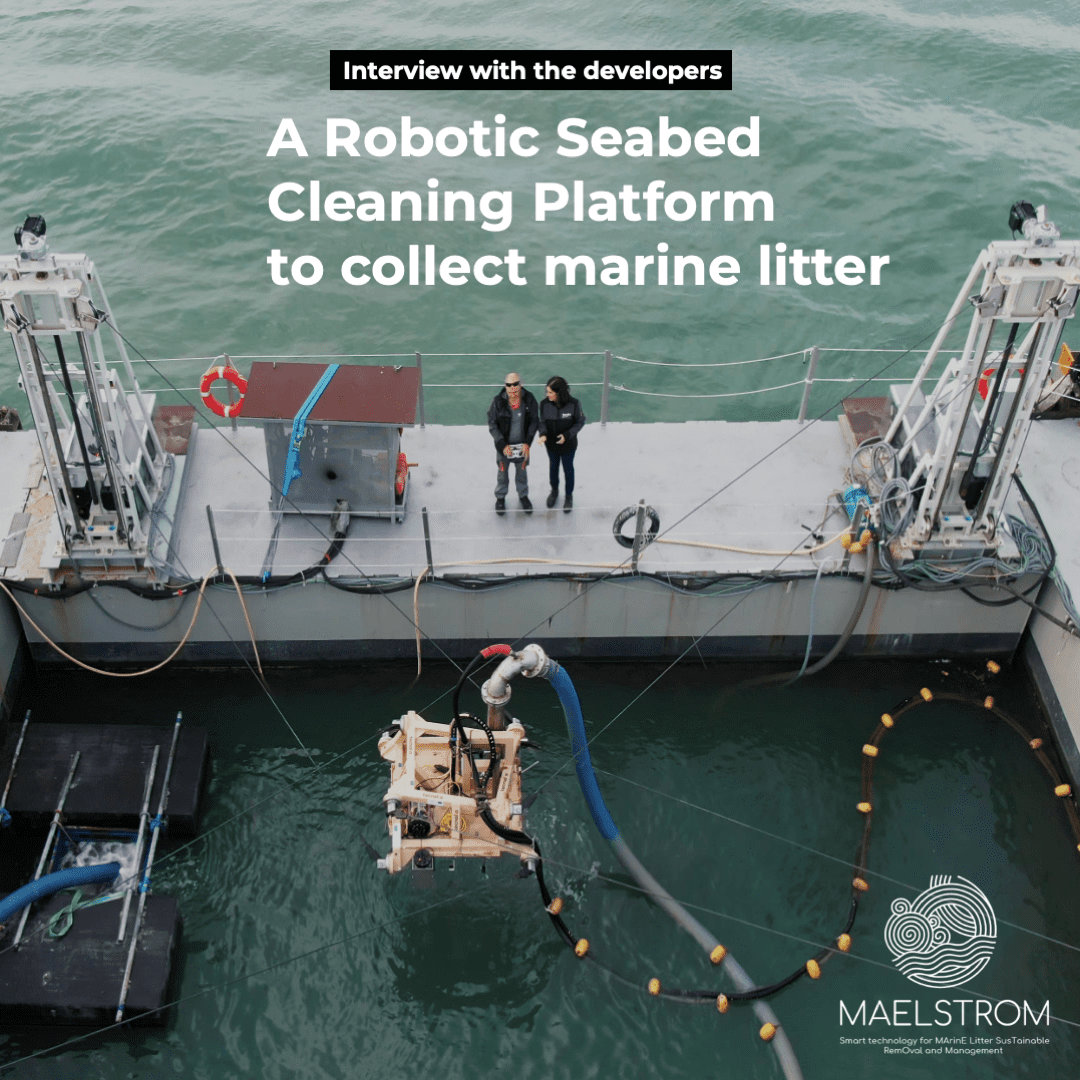
It collects marine litter from the seabed, up to twenty meters deep, without harming ecosystems thanks to an innovative AI system which selectively identifies objects to be removed – this is our MAELSTROM’s Robotic Seabed Cleaning Platform, developed by partners Tecnalia, CNRS-LIRMM and Servizi Tecnici.
The Robotic Seabed Cleaning Platform is currently implemented in the Venice Lagoon where our experts have been testing and verifying the entire mechanism. By adjusting the length of its eight cables, the robot’s end effector position can be precisely controlled, despite the currents. The cable robot’s frame integrates a set of sensors and cameras for manual, automatic and teleoperated operations and two cleaning tools: a gripper to lift up to 130 kg of marine litter (large items like bikes, households, tyres, containers, nets…) and a water-vacuum hose that allows for the removal of small debris on the seabed as well as floating plastics in the lower water column.
But how did this technology came about? How does it manage to respect the environment in which it operates and what are its current limitations?
Today we are delving into these and other questions with the leading implementers of MAELSTROM’s Robotic Seabed Cleaning Platform, so that you can also get to know it!
Why did you focus on the seabed litter, and which are the main issues regarding its removal?
Damien Sallé, Coordinator of Robotics & Automation at TECNALIA: Marine litter is a global problem. The first action should be to stop using and throwing plastics and litter. This said, there is plenty of legacy litter already in the environment that needs to be removed to avoid further degradation and contamination of the ecosystems and food chain.
For marine litter, it has been estimated that 86 million tonnes of plastics have accumulated in the world’s oceans, while 4.6-12.7 million tonnes are added every year. Floating litter counts for only 1% of this amount, the rest is most probably either laying on the seabed or having been degraded in micro and nano plastics having potentially been eaten by marine life. Some studies also point out that the majority of the seabed marine litter is found in shallow waters, close to the coast and the rivers, which is logical since these are the main entries of litter in the oceans.
Many initiatives are already ongoing for the removal of marine litter on the surface of the oceans, rivers or waterways but for the marine litter lying on the seabed, no real breakthrough has been achieved yet. Indeed, it’s much more difficult to localize it and to remove it.
Dr Sallé, from what were you inspired by to develop the Robotic Seabed Cleaning Platform idea?
We identified very few examples of technologies or activities of marine litter removal on the seabed. For example, fishermen can go “fish for litter” with their trawling nets, but can only do it in authorized sandy areas, and by this process have a huge negative impact on the ecosystems. On the other hand, divers make some actions of underwater clean-ups such as “diving against debris” initiative. These are great for consciousness raising and engaging local communities but have a very limited impact on the issue of marine litter removal at global scale.
There are some research projects using underwater robots (ROV) with a manipulator arm to pick a plastic object on the seabed. This can sound like a good solution, but it also has limitations: controlling a ROV and stabilizing it in the current to be able to make the picking is a very slow operation. Also, the weight of the object that such a system can pick up is limited and it requires quite some time to move each litter object back to the surface. We found this as being a relevant solution for high depths, but not efficient enough to be used to clean a hotspot in shallow waters.
Based on these insights, we decided to focus on a solution that would be very efficient to remove marine litter objects from the seabed of shallow waters. Since coastal areas host high levels of biodiversity in a fragile ecosystem, any automated marine litter removal technology has to be very selective to minimize its impact on the ecosystem. These were the two main targets that we had in mind during the process of designing the Robotic Seabed Cleaning Platform.
How did you move on into the design process? And in which way does the platform manage to avoid harming the ecosystems in which operates?
Damien Sallé, Coordinator of Robotics & Automation at TECNALIA: During the design process, we quickly discarded the ROV for their low efficiency. We also thought about using mobile robots that would move over the seabed with legs or wheels, but those systems would have strongly damaged the ecosystem. Then an idea came to our minds: combine the concept of cable driven robots (that Tecnalia and CNRS-LIRMM are co-developing and are used in the industry to manipulate objects in very large workspaces) with a floating platform that would support the underwater cable robot. This would create a kind of accurate and fast underwater crane that could integrate the cleaning devices (gripper, aspiration, hook etc). Since we operate from the surface and activate the removal tools only when needed, we can achieve a high selectivity and thus minimize the impact on the ecosystem. Moreover, since the cable robot is stiff and fast, we can lift heavy objects and clean quickly, so we also achieve efficiency. This is what we have invented and patented: a Robotic Seabed Cleaning Platform. It is a proposition we make to the world: to remove marine litter from the seabed of shallow waters!
Mariola Rodríguez, Project Manager at TECNALIA and Coordinator of the development of the Seabed Cleaning Cable Robot within MAELSTROM project: The innovation of the underwater cable robot that TECNALIA has patented is focused on the decision of where to locate the winches and the pulleys in the floating barge and on the design of the underwater robot frame with the aim of fulling the requirements of the application. The innovative design is composed of 8 synchronous winches that are rigidly fixed to 4 metallic posts mounting in pairs. The end of the cable that goes out of the winch is guided by pulleys to a vertical movable carriage. This vertical movable carriage has a vertical movement from the top to the bottom and from the bottom to the top of the post creating a reconfigurable cable robot. The reconfiguration capability of the underwater cable robot allows having the robot frame out of the water for assembling/mounting and maintenance operations and for safely translating the floating barge from spot to spot (parking position) and also having the robot inside the water for marine litter removal operations (working position). Moreover, the tensions of the 8 cables are monitored in real-time in the User Interface and if their values are out of the safety range defined, an error signal will appear and the cable robot will stop. Those advantages summed to the fact the underwater cable robot is easy to assemble, set-up and maintain, defines the good operability of the robot, a feature that must be highlighted.
The underwater cable robot has been designed to work until 20 m depth, to maximize its working space at different depths and its design is independent of the type and dimensions of the pontoon which allow its assembly in many different types of floating barges. The robot frame has a compact size to avoid collisions with any object (rocks, …) located on the seabed and to allow greater maneuverability. Moreover, it has been designed to support high water current forces at different depths, which makes it suitable for working in the peculiar conditions of the Venice Lagoon.
The underwater cable robot features high efficiency in the seabed cleaning process, as the robot’s frame can be moved accurately on the wavy seabed surface, and the cleaning devices actuated in a selective manner to ensure environmental sustainability.
The cable robot’s frame can be either remotely controlled by an operator – that targets each identified item and decides when to activate the collection tool – or controlled by an autonomous motion controller based on artificial intelligence, capable of identifying the marine litter item and choosing the most appropriate removal device, thus, avoiding wiping the seabed indiscriminately.
Regarding the use of the Robotic Seabed Cleaning Platform: how is the system controlled?
Marc Gouttefarde, CNRS Research Director at the LIRMM (CNRS – Univ. Montpellier, France) within the MAELSTROM project: The Robotic Seabed Cleaning Platform is an underwater cable-driven robot, which means that it is actuated by eight cables, attached to four poles located at the surface, on a floating barge. Each cable length is managed by a motorized winch, controlled by a computer. The position and orientation of the robot gripper is then defined by the lengths of the eight cables. The software developed for MAELSTROM’s computes in real time the geographic position of the robot, thanks to Real Time Kinematic (RTK) GPS and to several Inertial Measurement Units – devices which measure and report the position and orientation, respectively, while also monitoring and controlling the winches.
Moreover, the position of the robot is indicated on the bathymetric map of the seabed, where the position of the waste items is also depicted. The robot can move either in automatic mode (the software determines its own trajectory to reach the litter) or in manual mode (an operator pilots the robot with a joystick and the computer automatically manages the lengths of the cables). During every movement of the robot under the water, an embedded smart camera, combined with an acoustic sensor, scans the seabed to measure the depth (bathymetry) and to detect marine litter. These data are georeferenced and are used to update the map in real time.
How does the system recognize the waste to be collected, and which are the remaining challenges in this area?
Cyril Barrelet, Ph.D. student at the LIRMM (CNRS – Univ. Montpellier, France) within the MAELSTROM project: In manual mode, the robot is teleoperated by an operator that looks at various cameras and sensors to identify the litter item and pilots the robot to pick it.
To ease the work of this operator, we have also developed an automatic mode, in which the litter is detected by a video camera that scans the seabed, seeking for marine litter. During the scan, an Artificial Intelligence algorithm processes the images to automatically localize and identify marine debris (plastic bags, tires, bottles, etc.). We previously trained this AI algorithm on a database of thousands of images containing litter items that were manually localized and identified. The large number and variability of images allows the AI to recognize debris in various environments and acquisition conditions. Once the waste is detected, the image is sent to a human operator for final validation. The robot then reaches the position to be ready for debris removal by grasping or suction.
The remaining challenge is the turbidity of the water, which considerably reduces visibility in a coastal environment. We are currently working on this topic and also on the improvement of AI in new environments, in particular when few training images are available.
Till now, we haven’t talked about the platform supporting the robot. How was it designed and which are its main features?
Nicola Ferrari, Hydraulic and Naval Engineer, ST – Servizi Tecnici S.r.l, within the MAELSTROM project: The platform was designed to be used in the Venice lagoon and around coastal areas, but it can also be implemented in other type of locations. The modular barge that supports the weight and the dimensions of the cable robot was designed starting from existing certified modules from the naval division of ST, used in external shipyards.
The shape of the platform was built based on the dimensions of available certified modules for coastal sea utilization and considered the need to have an integrated protected basin inside the hull. The 2.45 m module width module allowed for the construction of an internal basin with the appropriate dimensions needed for the operativity of the cable robot.The construction of a reusable pin-connected support made the assembling of modules fast and safe.
To conclude, a specific stability booklet (approved from RINA, an Italian organization dealing with naval classification) and the navigation documents of every single module allow for the platform navigation compliantly with the existing legislation on the matter.
Dr Ferrari, which were the challenges of working in the context of the Venice Lagoon?
The Venice Lagoon has peculiar characteristics: strong currents, shallow water in the navigation borders of downtown canals and depth up to 12 m in the port and 20 m in the coastal area. Those represented operational conditions that had to be considered during the design of the platform.
We have equipped the platform with a mooring system with hydraulic spuds for the central lagoon locations with water depth up to 12 m (all the canals near the cleaning zone at Sacca Fisola and the Arsenale docks have a water depth of 5 m). This system is very fast and stable and has been used even for precision positioning tests with the help of Differential GPS (DGPS) present on board.